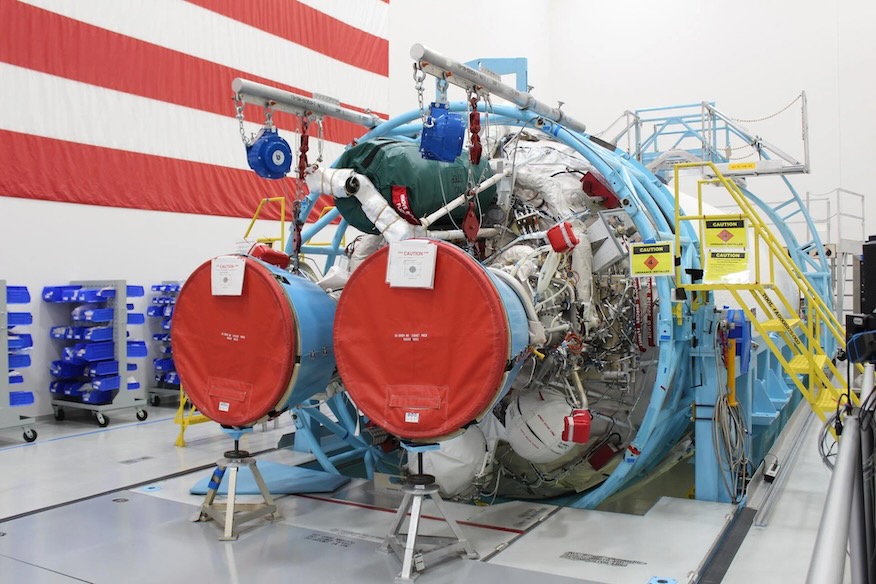
A rocket engine with an extended pedigree marked an enormous milestone on Monday. It’s 60 years because the hydrogen-fueled RL10 engine debuted onboard a Centaur higher stage launched from Cape Canaveral on Nov. 27, 1963.
With that first launch, the RL10 engine, at present manufactured by Aerojet Rocketdyne, turned the primary engine powered by a mixture of liquid hydrogen and liquid oxygen to be fired in area. The milestone got here at a pivotal time for the USA, because it was simply 5 days after the assassination of former President John F. Kennedy.
Since that time 60 years in the past, 522 RL10 engines have flown in area, with the lion’s share of these flights aboard United Launch Alliance’s (ULA) Delta and Atlas rockets. These engines energy the Delta Cryogenic Second Stage and Centaur higher stage respectively.
“Centaur and the RL10 have made it potential for us to launch spacecraft at higher dimension and weight over any of the opposite higher stage designs in use,” stated Gary Wentz, ULA vp of presidency and industrial applications, throughout a media occasion celebrating the milestone. “It has delivered unbelievable missions to the Solar, our Moon, asteroids, each planet within the [solar] system.”
The engine was developed by Pratt & Whitney within the late Nineteen Fifties by the oversight of NASA’s Lewis Analysis Middle, which was renamed the NASA John H. Glenn Analysis Middle at Lewis Subject in 1999. Centaur was initially developed by Basic Dynamics.
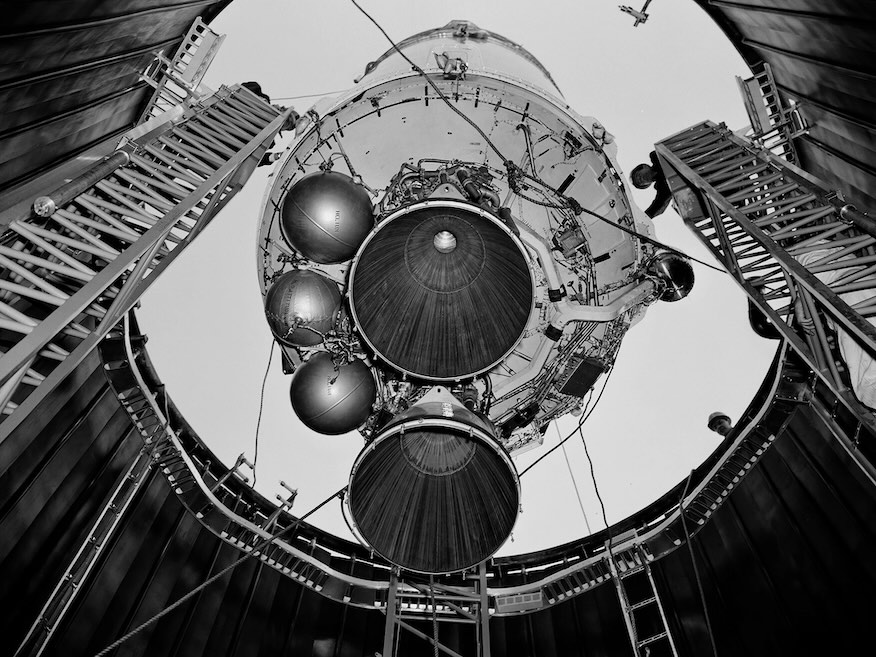
The mixture helped show the viability of liquid oxygen and liquid hydrogen as a propellant mixture for future launch autos. The RL10s themselves would go on for use aboard the Saturn 1, Atlas, Titan and Delta rockets.
The engine additionally loved use onboard the experimental suborbital automobile, the DC-X, which was utilized by NASA and the Division of Protection to display a vertical rocket touchdown.
“It’s very thrilling to be at 60 years and it’s a testomony to the unimaginable teamwork that’s gone on between Aerojet Rocketdyne and ULA over all these years, a testomony to all of the individuals who labored on this product all these years and an unimaginable design that was initially specified by the lat Nineteen Fifties,” stated Jim Maus, Aerojet Rocketdyne vp of program execution and integration.
Maus stated regardless of the successes they’ve seen over a whole lot of engine flights, they proceed to lean on ULA’s motto of specializing in launching one after the other.
“After we go to launch day, we’re very targeted on that day’s launch,” Maus stated. “And so, whenever you come to an enormous milestone, you form of stand again and acknowledge, you recognize, have a look at all that we’ve completed. So, it’s nice to be a part of the crew that does that and we’re actually thrilled to be at 60 years.”
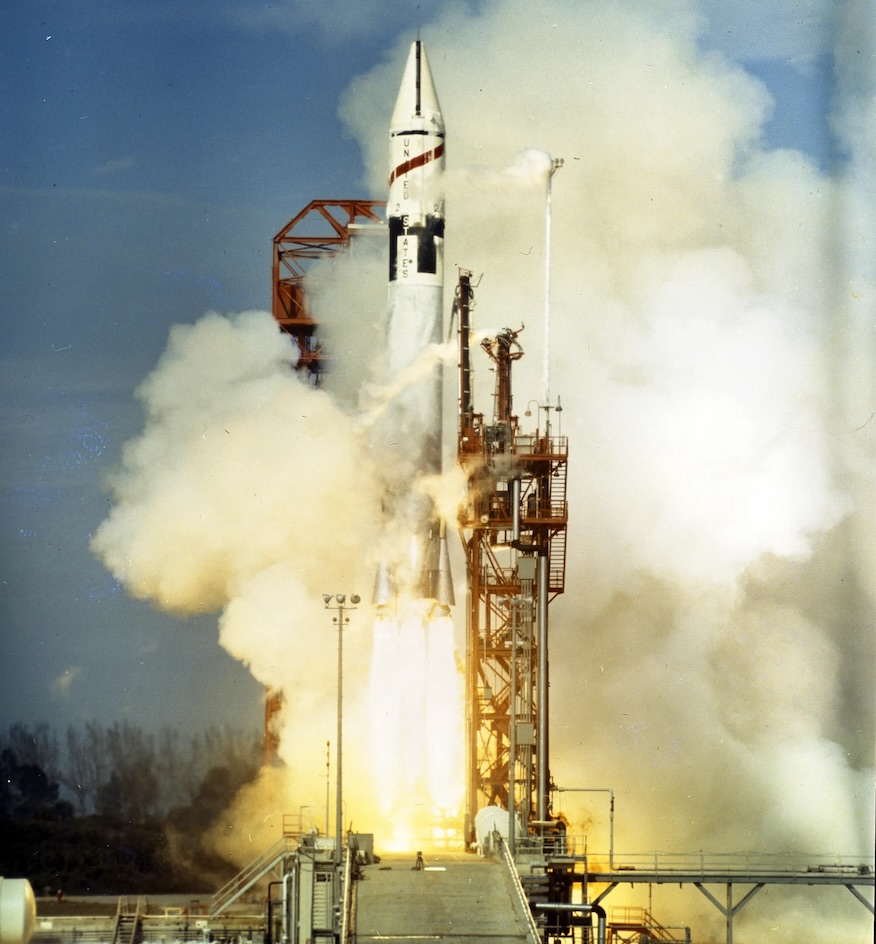
Evolving the RL10
At present, there are two variants of the RL10 in use: the RL10C-1-1 on ULA’s Atlas rockets and the RL10B-2, which is used on the ULA Delta 4 Heavy and NASA Area Launch System (SLS) rockets.
The latter variant has a restricted life although since there is just one extra Delta 4 Heavy rocket, which is scheduled to launch in 2024 on a mission for the Nationwide Reconnaissance Workplace (NRO). A single RL10B-2 can be used on the SLS’s Interim Cryogenic Propulsion Stage (ICPS) for the primary three Artemis missions to the Moon.
Later variations of the SLS will use the Exploration Higher Stage, which is being engineered by Boeing. That shall be powered by 4 RL10C-3 engines, which collectively will present greater than 97,000 kilos (431kN) thrust. For comparability, the only RL10B-2 on the Artemis 1 ICPS produced about 24,750 kilos (110kN) of thrust.
So far, Maus stated there have been eight main upgrades of the RL10 engine. The following main iteration of the engine, the RL10C-X, which remains to be in improvement, will energy future model of ULA’s forthcoming Vulcan rocket.
The largest change seen with this model of the engine comes by its use of additive manufacturing methods, extra generally generally known as 3D printing.
“We’re already flying the RL10 with an additive manufactured injector, however now we’re doing an additive manufactured thrust chamber and we’re going by that certification proper now,” Maus stated. “That engine shall be delivering the best efficiency of what we now have out there in safety as we speak and can lengthen the lifetime of the RL10 into the long run.”
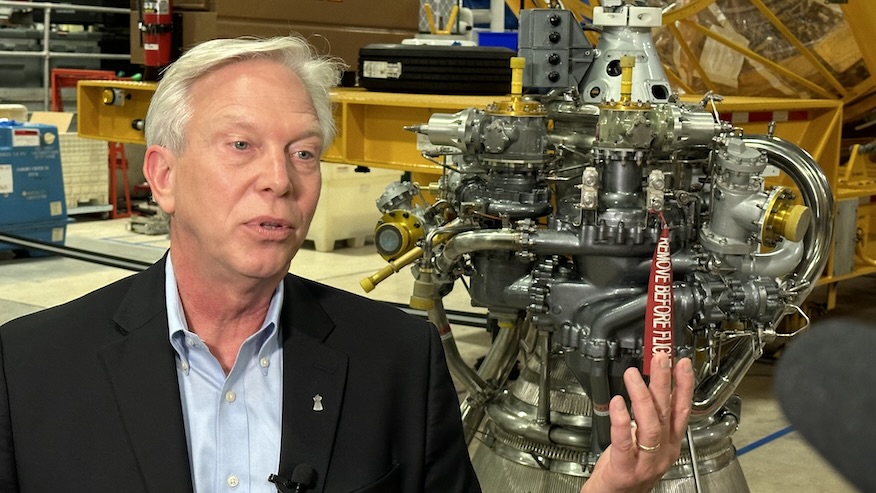
Maus added that the brand new manufacturing methods may even convey value financial savings, however declined to enter specifics on the drivers of the price discount.
“It’s been a major enchancment in value on the chamber of the engine. We’re additionally placing a big carbon silicone nozzle on it, that’s pushing up the ISP to present us good efficiency,” Maus stated. “After which, the turbo equipment and what I’ll name the powerhead and the spine of the engine is equivalent to what we’ve been flying on the steadiness of the stock. So, that it’s going to proceed to delver the very excessive reliability on day one, launch one.”
The particular date of launch one nonetheless stays TBD, however Maus stated they’re aiming to debut the RL10C-X in 2025 on a ULA Vulcan rocket. That stated, Maus famous that they’ve orders for the present RL10C-1-1 engines by 2026.
Each NASA and ULA are driving what Maus described as a backlog of greater than 150 engines, that are a mixture of the legacy variations in addition to the X-C variants with the additive manufactured options. He stated NASA remains to be making a willpower on whether or not they need to buy extra of the legacy engines or start to purchase engines utilizing the additive manufacturing expertise for future Artemis missions.
In a typical 12 months, Maus stated Aerojet Rocketdyne produces between 16 and 18 engines, however with the incorporation of extra additive manufacturing into their manufacturing line, they’re ramping as much as 40 engines yearly.
“We shortly acknowledged that by 3D printing the combustion chamber, we may actually make an enormous change to the price of the engine and the reliance readily available fabricators,” Maus stated. “So, shifting away from the stainless-steel fabrication to the 3D printed copper, we’re in a position to now construct geometries we couldn’t have constructed in any other case with additive manufacturing. After which, we’re in a position to produce the engine now with the excessive volumes and the excessive charges that ULA wants.”
Traditional engine, new rocket
In lower than a month, ULA plans to debut its Vulcan rocket. The mission, dubbed Vulcan Cert-1, will use a pair of RL10C-1-1A engines to energy the Centaur 5 higher stage and ship Astrobotic’s Peregrine lunar lander on its strategy to the Moon.
After delivery an upgraded Centaur 5 from its manufacturing facility in Decatur, Alabama, ULA built-in higher stage onto the Vulcan booster on Nov. 19. The mission is about to fly no sooner than Dec. 24, 2023.
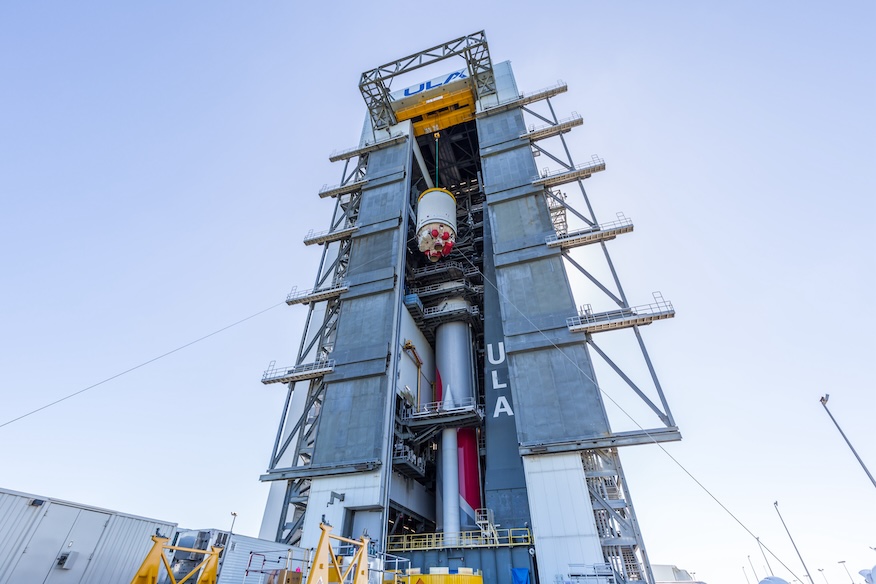
ULA is making ready for a moist gown rehearsal within the first half of December throughout which the totally built-in Vulcan rocket shall be rolled out to the launch pad and fueled because it if had been launching. Maus stated Aerojet Rocketdyne engineers shall be on headsets throughout that fueling take a look at to observe the Centaur and the way the engine is cooled and conditioned as will probably be on launch day.
“Now we have engineers all the information coming off the engine throughout moist gown rehearsal and we are able to just about perceive in actual time that all the things goes proper,” Maus stated. “However then in fact, there’s an information evaluate that’ll come after that to make sure that all the things carried out as required.”
Ron Fortson, the director and basic supervisor of launch operations for ULA, stated they’ll then roll the rocket out to the launch pad the day earlier than liftoff and get on console to start the countdown about 12 hours forward of time.
Fortson stated integrating the RL10C-1-1A with the Vulcan automobile went easily.
“The whole lot went effectively in our manufacturing facility after which right here, it already comes totally assembled and we simply mate it with our rocket and we’re able to go,” Fortson stated. “So, it’s been an important exercise.”
Fortson stated he and the crew at ULA have been working carefully with Aerojet Rocketdyne as they work in direction of the debut of the RL10C-X engine in a few years.
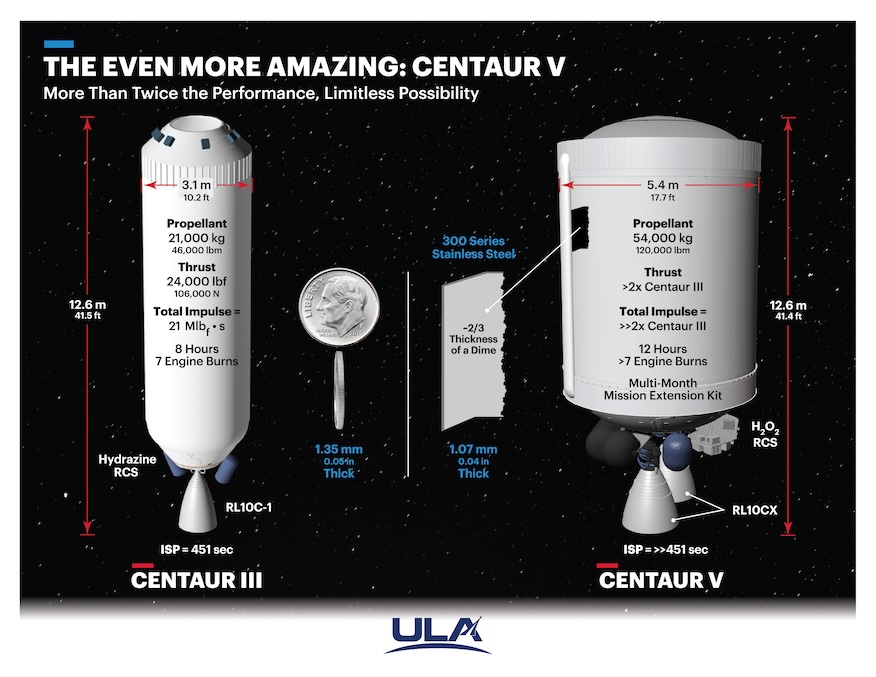
“We’re working very carefully with them on their design and their testing. As soon as that’s all accomplished, we’ll be wanting ahead to really simply integrating it onto our Vulcan rocket,” Fortson stated. “After which in fact, we’ll be all of our missions which are coming ahead when it comes to what these necessities are and ensuring we are able to fulfill these necessities with this new engine.”
He stated there possible received’t be a selected flight profile that may required for the debut of the RL10C-X on Vulcan, including that “This engine’s going to be able to doing something we want it to do.”
“I feel no matter necessities we now have for it, we’re assured that this engine will have the ability to fulfill it,” Fortson stated.
“Now we have a philosophy of take a look at such as you fly, which implies the engine will solely see in flight that which it has skilled on the bottom throughout the limits of what we are able to take a look at or analyze,” Maus stated. “So, we’ve been by all of that testing during the last a number of years to grasp how the engine operates within the Vulcan scheme.”
Maus stated as they sit up for flying the RL10 on new rockets and in new iterations, they sit up for one other key milestone: flying people through the Industrial Crew and the Artemis applications.
“We’ve been bringing astronauts all the way down to West Palm Seashore, to our facility to speak to our crew in regards to the actuality of what we ship and it’s very motivating for us to see our passengers standing in entrance of the room, telling us about how a lot they’re relying upon us,” Maus stated. “However the actuality is, we design and construct a extremely dependable product and it has demonstrated its reliability.”